IDM Upgrading Coal Slime Drying Machine
High-Temperature Dryer and Kiln Technology Converts Coal Ash to Lightweight Ceramic Aggregate.
ABSTRACT
Upgrading brown coal is the method used to increase the quality of low-rank coals. This method typically uses heavy oil to be mixed to close the pores resulting in indication, subsequent to the upgrading of brown coal. Closing of the pores (coating) is used in the form of low sulfur waxy residue useful residue lining the pores of coal that after brown coal upgrading process of re-absorption of moisture will be smaller.
This coating method itself on its principle of maintaining the quality of coal as a high calorific value and inherent moisture content of the coal after the brown coal upgrading process is maintained. The results of the analysis of the process of upgrading coal residue obtained mixture percentage and the most optimal residence time is residue 1% (29% coal) and 15min residence time for the residue.
The results of the analysis of the percentage of moisture produced results in inherent moisture of coal upgrading between Kalimantan and low sulfur waxy residue that is 0.89% for a 10-minute ADB and ADB 0.80% for 15 minutes. There has also
been an increase in the calorific value of coal Aceh optimal 4920.12 kcal/kg to 6709.86kcal/kg (10 min) and 6674.34kcal/kg.
The percentage of re-absorption of moisture coal after the brown coal upgrading process by using low sulfur waxy residue
has a smaller percentage of absorption.
1. INTRODUCTION
Coal in Indonesia is mostly used for the needs of electricity generation in steam power plants, the textile industry, paper industry, and the cement industry, in addition to its more economical price and a large number of reserves. (Megasari, 2008). Low-rank coal (brown coal) is not widely used due to its moisture content coal is quite high about more than 40%. In addition to the high moisture content, brown coal can This causes self-burning, and also most brown coal contains low levels of sulfur and ash.
With the value of low sulfur and ash content, it can be used to make brown coal into high quality by upgrading brown coal using a mixture of residues in the form of asphalt and low sulfur waxy residue so that the coating process occurs [1].
Upgrading brown coal
Various methods have been developed to reduce the moisture content of low-rank coal such as drying at a certain location. However, this method is considered less effective because, during the drying process, the moisture content in coal will evaporate but when the coal is left at room temperature the content of coal moisture will increase and even return to its original position. This is due to the condition of the coal pores After drying, it expands making it easier for water vapor or water to enter back into the coal. This problem can be solved by doing special treatment of the coal pores after it is done drying by using compounds that can close the pores of coal [2]
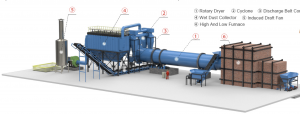
The compound used to overcome the above problems is to use of heavy oil compounds namely asphalt and low sulfur waxy residue (LSWR). These heavy oil compounds can absorb into the pores of coal when heated using a light oil mixture. Heavy oil which is the second compound can prevent the occurrence of self-burning in low-rank coal because this heavy oil is absorbed
into the coal pores. By using this heavy oil compound, it can improve the quality of coal low rank that has the largest reserves in the world [3].
The upgrading system of brown coal using heavy oil is included in upgrading coal by means of coating (coating). The coil coating process itself is used to coat the coal so that the moisture being in free air cannot re-enter the coal it can affect the calorie level of the coal. With the coal coating system combined with sweating, it is hoped that
can be used in utilizing young coal which is spread very much in Indonesia [4].
2. RESEARCH METHOD
The research method used is to conduct a literature study related to the brown upgrading analysis of coals and coatings. After conducting a literature study, further research on a laboratory scale was carried out to solve the problem formulation. Laboratory research was carried out to analyze coal from upgrading brown coal so that it can be used. The secondary data in this study is the analysis of inherent moisture, analysis of value heat, and aging test analysis. While the supporting data in this study include the initial coal proximate analysis which is used as initial data that will be used as a reference in research on the results of upgrading brown coal.
3. RESULTS AND DISCUSSION
The upgrading process of brown coal is a process of improving the quality of low-rank coal. In this research, the upgrading process of brown coal has the function of improving the quality of low-rank coal and coating (coating) using a residue in the form of low sulfur waxy residue [5]
The upgrading process of brown coal which includes distillation and drying has an effect on the coating as seen from the decrease in inherent moisture, the increase in the calorific value of coal, and the difference in the value of coal calories with the addition of residues that have the same inherent moisture and absorption percentage return moisture which has a smaller value.
3.1.The Effect of Brown Coal Upgrading on Inherent Moisture The upgrading process of brown coal using asphalt and low sulfur waxy residue has an effect on inherent moisture. The effect of upgrading brown coal can reduce the inherent moisture of the resulting coal upgrading. Where the process can reduce the inherent moisture from 15.8% to <2% ADB. The effect of low sulfur waxy residue in the upgrading process on inherent moisture is shown in Figure 1.
showed that the reduction of inherent moisture by using a mixture of residues resulted in inherent less moisture than Non-UBC and UBC coal without residue. The addition of 0.3% residue resulted in A smaller decrease in inherent moisture was 0.89% ADB (10 minutes) and 0.80% ADB (15 minutes).
The difference in inherent moisture between Non-UBC (before UBC) and after UBC using residue is 14.91% ADB(10 minutes) and 15.00% adb (Appendix C). This is because the residue is an organic compound that has the same chemical properties as coal, so when it is adsorbed into the pores of the coal the residue will dry and replace the position of inherent moisture [6]. In addition, it can be seen that the longer the time the upgrading process can increase the decrease in inherent moisture so the time can also affect the brown coal upgrading process.
3.2. Effect of Upgrading Brown Coal on the Calorific Value of Coal
The relationship between low sulfur waxy residue on the calorific value of coal (Figure 3) shows that the increase in the value of
calories using residue mixture produces a large calorific value compared to UBC without residue and Non-UBC. The percentage of residue that produces a greater calorific value uses a percentage of 1%, namely from 4920.12 kcal/kg to 6709.86 kcal/kg (10 minutes) and 6674.34 kcal/kg (15 minutes) (Appendix D).
This is happening because the low sulfur waxy residue is absorbed into the pores or coats the pores giving additional calorific value in coal, where the low sulfur waxy residue has its own calorific value. If low sulfur waxy residue is If you mix more and more, then the adsorbed residue will then dry into the pores so that it occurs coating which causes the calorific value of coal to increase [7]. In addition, the residence time during the process of upgrading brown coal also affects the calorific value of coal. The longer the upgrade process time, the resulting in higher the calorific value of coal.