Blowdown Boilers aplicated
Blowdown Boilers
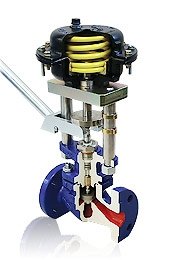
Water kettle from feedwater still contains impurities which if accumulated in the boiler can reduce boiler performance. For that blowdown is needed to clean the dirt. On the other hand, the impurities can also affect the quality of the steam coming out of the boiler towards the turbine. If the steam produced by the boiler still contains water and dirt it will damage the turbine, so that the steam purification process is needed so that the steam entering the turbine is really pure steam.
- Introduction
Steam boilers or boilers, also known as steam producers, are a device used to produce steam ( steam ) for the purposes of power generation, process and heating in the industry. Here is one of the boiler system products in the industry:
Water supplied to the boiler from feedwater (boiler water filler) still containsimpurities in the form of suspensions, salts, mud, and solids. The dirt can settle and accumulate in the boiler if the boiler operates continuously. Increased concentrations of impurities in the form of solids dissolved in kettle water can be mixed with steam (steam ), causing damage to pipes, steam traps, as well as other equipment operations, especially in turbines.
The increase in concentration in the form of a suspension in the form of sludge (sludge ) will affect the boiler efficiency and heat transfer process.
To overcome the above problems, the water in the boiler needs to be cleaned or ” blow down ” periodically to control the level of concentrate in the boiler. Blowdown on boiler water surface ( surface water blowdown ) is usually carried out periodically to reduce the amount of dissolved solids in the boiler water. The blowdown at the bottom of the boiler ( bottom blowdown ) serves to remove dirt in the form of sludge ( sludge ) that settles at the bottom of the boiler.
Periodic boilers are very important. However, improper blowdown can lead to increased fuel consumption, additional other chemical treatments ( chemical treatment) and heat loss .
- Advantages Blowdon Boiler
- Reducing the use of water, fuel and chemical treatment
- Reducing maintenance and repair costs
- The steam is more efficient and cleaner
- Reducing operating costs (reduction in fuel consumption, chemical treatment andheat loss )
- Minimize energy loss up to 2% of the total energy requirements needed.
Equation
To calculate the ratio of the number of blowdowns needed, calculated using the formula:
Where:
C feedwater = Measured chemical concentration in feed water
C blowdown = Measured chemical concentration in the boiler
The concentration limit allowed for boiler water from feedwater is determined based on the standards issued by the American Boiler Manufacturers Association (ABMA), as follows:
- Automatic Blowdon Control
There are two types of blowdown boilers, namely manual and automatic . However,manual blowdown has disadvantages such as:
- Routinely have to check water samples
- Routinely have to do blowdown adjustments
- You cannot know exactly when and how long to use blowdown
- Can not directly respond to changes in feed water conditions
The advantages of using automatic blowdown are as follows:
- Observation of water conductivity can be done constantly
- Reducing operational costs
- Can adjust the rate of blowdown to water chemicals
- Can set the blowdown rate near the maximum limit of the desired dissolved level
- Changing manual blowdown to automatic blowdown can reduce boiler energy use to 2-5% and reduce boiler waterlosses to 20%
- Blowdon Heat Recovery Unit
Taking heat loss in a boiler blowdown can be done in two ways, namely:
- Flash Tank System
The flash tank system is shown in the figure below which can be used when the financing and operations issued must be reduced to a minimum. In this system,blowdown is flowed through a flash tank, then it will be converted into low pressure steam. This low pressure steam is very suitable for the type of deaerator or makeup water heater.
In the diagram above flash steam is only used to preheat the makeup water in an atmospheric deaerator . The heat condensate generated from the blowdown is flowed towards the drain .
- Heat Exchanger
- Flash Tank System-Heat Exchanger (Combined)
The system below shows the process of Flash Tank System Heat Exchanger .The blowdown temperature leaving the flash tank is usually still above 220 0 F. The heat from the flash blowdown can be used to heat the makeup water by flowing it to the heat exchanger, while cooling the blowdown simultaneously.Heating makeup water on the boiler can save fuel costs.
With the addition of cold water storage tanks and circulation pumps through a heat exchanger, it does not require cold makeup water and blowdown to occur at the same time.
Related articles:
Get to know Blowdown Boiler Boiler Furnace and design of FiresideBasic Steam Generator